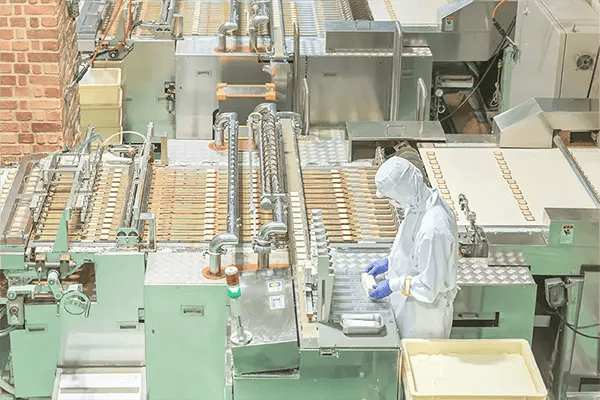
Stelo's Real-Time Efficiencies Keep Orders and Operations Flowing
US Foods is one of America’s largest food processing and distributor companies, serving independent and multi-unit restaurants, healthcare, hospitality, government, and educational institutions. US Foods offers more than 350,000 products and they employ approximately 25,000 people in more than 60 locations nationwide. They operate stockyards and food processing plants across the United States, processing nearly 70,000 transactions daily between each processing plant and headquarters.
The Stockyards division consists of a network of production sites where meat and fish products are labeled and processed for national retail and hospitality customers. Before Stelo, sales orders were sent in a single batch from the national headquarters to all processing facilities, and once the orders were processed, the inventory transaction details were sent back to headquarters. However, if the network connection was compromised in any way, orders would get backlogged, and worse, production would cease. Stelo minimized processing time and enabled processing to continue even with failed network connections.
Need
All data from the local production floors was directly connected to the national mainframe IBM for i (formerly iSeries) database. Because of the dependency on the network, any break within the network created a backlog of orders. Data could not be transferred when the network was down and would cease production at all seven facilities until the connectivity was resolved. Therefore, this company needed a reliable and instantaneous solution to send inventory data to the main computer system that was not dependent on a continuous network connection.
Solution
Stelo is now deployed at each processing facility with a Windows-based middle tier that connects to the mainframe IBM for i. Proactive email notifications are configured to alert DBAs to any potential connectivity issues. The scales on the production floor record a variety of processing information such as weight, country of origin and ingredient descriptions. The scale data is sent to a local 64-bit Windows-based SQL middle tier, then passed up to the national headquarters’ IBM for i mainframe. From headquarters, the daily orders are sent to each individual cutting facility. Stelo minimized processing time and enabled processing to continue even with failed network connections.
Learn More
Results
Business Dashboards
Individual locations have instant access to order data speeds production.
Continuous Connectivity
Production flows have real-time continuous connectivity.
Automation
Proactive email notifications help thwart potential issues.
Benefits
Production Can Begin Immediately
Stelo has allowed US Foods to send concise regional order lists to each facility instead of transmitting a cumbersome national order list. The facilities can now begin production immediately rather than sorting through a master list.
Headquarters Can Stay in Business
If the network goes down at a particular processing location, headquarters can continue to send specific orders to other facilities independently.
Total Production Never Backlogs
Although the data replication occurs immediately, if there is a break in network connectivity between the iSeries and the local SQL servers, production can continue uninterrupted on the processing floor. The processing data is staged on the SQL server until the data connection is resolved, then sent to the iSeries.
Get Started
These three steps will help you ensure Stelo works for your needs, then seamlessly deploy your solution.
Schedule a Demo
Our expert consultants will guide you through the functionality of Stelo, using your intended data stores.
Try Stelo
Test the full capability of the software in your own environment for 15 days. No obligations.
Go Live
When you're ready, we can deploy your Stelo instance in under 24 hours with no disruptions to your operations.